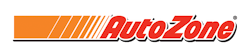
WHAT IT IS: Technician efficiency is the measure of a technician’s billable hours (booked time on the repair) compared to the actual hours needed to complete the work. Tech efficiency can be measured on a per-job basis or over a period of time (weekly, monthly, yearly). The efficiency figure shows the rate at which technicians get the job done once they begin working on the repair order.
HOW TO CALCULATE IT: Flat rate hours produced ÷ actual hours worked.
INDUSTRY AVERAGE: 80–99%
OPTIMAL BENCHMARK: 100%+. Ninety-four percent of shops surveyed with more than $1 million annual revenue track technician efficiency, and roughly 1 out of 3 of those shops report technician efficiency above 100 percent.
HOW TO IMPROVE IT: Many owners track KPIs such as technician efficiency, but few know what to do to improve it (or are simply scared to implement change). It’s not as frightening as the ledger may seem.
Let’s say your shop rate is $90 per hour. Your three technicians are inefficient by .3 a piece, and that adds up. That’s $30,000 of lost work per year.
How do you empower your technicians? Proper equipment is one of the main factors. Most heavy equipment needs to be updated every three to five years and regularly serviced and maintained in the interim. Diagnostic software, on the other hand, needs to be updated quarterly or better in order to keep up with the rapid pace of technology. Information is money, in other words. Be sure you make the most of both, have regular processes to ensure the tools and tech on the floor are as up to date as can be, and are ready to service the next customer rolling through your doors.
Properly training technicians is another way to ensure high efficiency. If they don’t know what they’re doing, you’re probably not the first to know. Be sure to keep easy and open communication about your techs’ abilities, and give them the opportunity to improve via trade shows and specialized training to bolster their skill set.
Average hours per repair order also affects efficiency. Informed, efficient service advisors enable your technicians to maximize their potential; inefficient advisors make for inefficient technicians, and you can’t afford either. The national average of hours per RO is roughly 1.8–2.4, but many shops can—and should—do better.
About the Author
Sponsored Content
The views and opinions expressed in this piece do not necessarily reflect those of 10 Missions Media and its associated brands.