Nobody would take a chance on Adam White.
Looking back on it all, White completely understands why: A substance abuser since the age of 11, the high school dropout bounced from job to job as he experimented with hard drugs.
As he tried for years to kick his habit, the one consistency in White’s life was automotive repair. His father was known as the best frame specialist in town, and White had been learning the trade throughout his youth.
Once White had managed to achieve three years of sobriety, in 2013, he applied to work as a technician at A.S.P.I. Motor Cars—a used car dealership in Dedham, Mass., that performs mechanical work on vehicles to be auctioned off.
“I knew his father, who is one of the best auto body frame guys I have ever known,” A.S.P.I. president Lou Tedeschi says. “I believed with a little help, this kid could be as good as his dad.”
Tedeschi says White has the uncanny ability to completely diagnose vehicles in his head, taking the car apart in his mind and mapping out exactly how he’ll fix it. That’s why, after White relapsed six months into his new job, Tedeschi didn’t abandon him, but instead sent him through a recovery program.
White has been clean since the day he exited that program (Aug. 27, 2013), and now he’s more than a technician—he’s Tedeschi’s “right hand man,” performing large repairs for the $2.3 million shop’s monthly output of 260 vehicles.
It means a lot that Lou took a chance on me. This is a great place and I love working here. I really owe a lot to Lou and I care about my job.
I don’t like to do anything half-assed. I want to see good results and I’ll take the extra 10 minutes to make sure a car is completely ready to go. I don’t like to rush things and put out something that’s going to come back. In the end, it reflects on myself and the company. When you do good work, people want to come back and they want you to work for them.
I come in when the shop opens at 9 a.m., meet with Lou and see what’s on the schedule for the day. For us, it’s not about the daily workload, but the week, so we have a whiteboard that tracks our different projects. Sometimes we will have a car that needs to be pushed out in a day, but most of these are our vehicles that we’re selling. We may be working on 10–15 vehicles a week in different aspects. Most of our service work is long term stuff that takes over a week to do.
There’s a variety of different problems that come in every day. A lot of them are electrical problems. We just had a dump truck with an electrical problem with the tail lights we had to figure out. Today I'm working on a truck with some light issues. And then we have a suspension we're getting ready to overhaul. We recondition vehicles from bumper to bumper. We go through the whole car with our scan tools, do a check-over for every system in the car, if it needs brakes, ball joints—whatever it needs. It’s really different from car to car.
Typically, we get a trade-in for a car that’s getting purchased off the lot, and it’s all rotted out and you couldn’t get any money for it the way it is, except for scrap metal. What I do every day is take those cars, fix all that rot and get the car looking good so we can take it to the auction and actually make some money on it, instead of giving it away for free. Something like that will take a few days to do if you’re replacing all the rocker panels, doing the wheel wells, stuff like that.
When a car comes in, Lou and I spend a lot of time on it before I pull anything out. Having two sets of eyes go over it helps. We’ll point out anything it needs using a paint marker, circling a spot or pointing out some rot. We’ll put together a parts list and order those right away.
A.S.P.I. MOTOR CARS
LOCATION: Dedham, Mass.
SIZE: 8,000 square feet
STAFF: 12 (6 technicians, 2 owners, 2 office personnel, 1 detailer, 1 service advisor)
NUMBER OF LIFTS: 5
AVERAGE MONTHLY CAR COUNT: 260
ANNUAL REVENUE: $2.3 million
Even on repairs I haven’t done before, I’ve always been able to look at something, take it apart, and put it back together in my head. I can see how the parts interact and work with each other. If you can understand how something works, you can diagnose what went wrong with it. If you can visualize how everything is working together, you can point out almost instantly what’s wrong with it.
If I don’t feel comfortable or know how to do a repair, I’ll talk to Lou. He has a lot of experience and most of the time he’s run into it before. So I get his help for a minute and he’ll guide me through it. One time usually does it and I’m good.
But I really do like to do things on my own. I do my homework before I start tearing into something. If it’s something I’m not familiar with, I'll Google it, get online, try to find a procedure for it, make sure I know what I’m doing before we start tearing into it.
Too many guys start tearing into stuff and then they get in over their head and realize they don’t have the specialty tools that they might need to do something. If you just start ripping stuff apart and don’t understand how it works, how are you supposed to put it back together? You have to be organized and spend some time on it.
When I take something apart, I take pictures along the way. I always take pictures before, after and during. A lot of times I'll have to go back to it as a reference. You'll rip one side apart and won’t get back to it for another week. It comes in handy to have that picture to go back to and look at it and see where that line was. It’s real helpful.
Every photo I’ve ever taken is on my auto backup. I take them with my phone, and then they get loaded into my Google account, which has way more storage space than my phone or computer. They just load up, and when my phone gets full I can delete them all and still have them. It helps me track a repair, and it’s also a good reference point for when I’m doing a similar repair in the future.
I also have boxes and cups labeled with parts. If I take out a part and don’t get back to it for six months, I want to have it labeled in a box, “left side, front,” with all the bolts in there with the fender and the lights and the moldings. Any time I take something apart like that, I box it up, put a piece of masking tape on it and label. You don’t want bolts lying all over the shop.
It’s the same procedure with wires. You’re not going to remember all the fifty different colors of wires in there, so we make a wiring diagram for each vehicle and label where these wires came off. Little things that take a couple minutes and save you a lot of headache down the line.
I try to make sure I got all the work done that needs to go out the door that day. I’ll stay late if I have to. Then I clean up. It’s important to leave yourself a clean workspace for the morning so you’re not cleaning yesterday’s mess. Prepping yourself for the next day saves so much time in the morning. Just spend 10 minutes setting up for it. Pull the car in and get what you need out so when you come in in the morning, you can go right at it.
About the Author
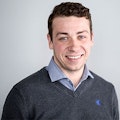