It wasn’t just a huge year for auto repair, for on-board diagnostics, for vehicle technology—1996 was the year that redefined Cliff Shenkel’s career.
When OBD-II was introduced to control vehicle emissions, technicians were suddenly working with computerized systems dealing with direct ignition and fuel injection in addition to regular maintenance and repairs.
“I got into diagnostics because nobody else wanted to do it,” he says. “It was new, and it required a lot of training and classes to fully understand.”
The education in electronics and vehicle technology Shenkel pursued 20 years ago has paid off, giving him a jump start on perfecting a diagnostic process that, he says, will guarantee him a job anywhere.
“There’s a gap between technology and what the average technician knows,” he says. “We’re getting to the point where we have to understand how capacitors and all these electronic components work in order to truly diagnose something.”
Because of his deep knowledge of diagnostics, Shenkel was recruited to work at Dwight’s Automotive & Tire in Nipomo, Calif., where he’s putting his lifelong dedication to diagnostics to work.
Dwight’s Automotive & Tire
—
Location: Nipomo, Calif.
Size: 3,500 square feet
Staff: 2 (1 technician, 1 owner)
Number of Lifts: 3
Average Monthly Car Count: 150
Annual Revenue: $350,000
We’re a smaller shop. There’s only two of us, and I usually work on 10 to 12 vehicles per day. Seventy-five percent of the time I can diagnose a vehicle in 30 minutes. If I don’t have an answer, I take a break from working on it because I start getting in a vicious circle. I do something mindless, something simple while still thinking about the vehicle, and then come back to it and usually find the problem within 15 minutes.
I’ve developed a procedure over the past 20 years that streamlines the diagnostic process for me. I start by test driving the car regardless of what the customer says the problem is, just to get a feel for what I think the problem might be. Then I will check for technical service bulletins (TSBs) or problems known to that vehicle if I haven’t experienced it before.
We have dozens of scan tools in the shop, so choosing the best scan tool boils down to experience. It’s knowing: “This has good coverage, this doesn’t; this scan tool lies, this scan tool doesn’t.” The best scan tools for any job are the factory ones, which make everything easier.
We work on Fords and Toyotas the most, so that’s why I bought a Ford scan tool and a Technical Information System Techstream Lite. For European vehicles, I usually grab the Snap-on ETHOS or the Autel DS708. I bought the Ross-Tech VCDS originally for my own VW, and that works great.
A lab scope is the easiest and fastest way to diagnose most problems. I use it as a backup to my scan tools to verify the problem. It does just about everything you’d want. The most common thing I use it for is motor problems. I use a current probe and the voltmeter on the lab scope almost daily. It just makes diagnosing motors and solenoids so fast and easy. And the faster I can get it figured out, the faster I can get the customer back in his or her vehicle.
To stay ahead in this game, you really have to think outside the box. The only thing stopping you is your imagination. I’ve been using the lab scope to test water movement in the radiator to see if the water pump is working. You can’t just follow the troubleshooting tree.
Reprogramming is a necessity now, and another addition to the diagnostic path. There are so many cars out there that reprogramming can fix. If I’m doing a 30-minute diagnosis and I think there’s nothing wrong with the car, but the check engine light is on, I need to step back. That’s when I research if a reflash is available.
Then I need to inform the customer that there’s a 75–80 percent chance a reflash will repair the vehicle, but there’s no real guarantee. Just because a car has a reflash, it’s not always recommended to reflash, because it could cause another problem. The problem with reflashing overall is a lot of manufacturers don’t tell you what the reflash does. It fixes the symptom, but it doesn’t tell you how it fixes the symptom or what it will affect.
That’s the other thing I need to be conscious of throughout the day: Scan tools can lie. In my experience, they lie 30 percent of the time. That’s why I have to back scans up with lab scope data.
There are two sides to a scan tool: There’s the manufacturer side and the OBD-II side. OBD-II is generic.Not too long ago I had an old Dodge pickup. The scan tool told me the oxygen sensor was reading one volt, which told me the car was running rich. But when I checked the actual oxygen system voltage, it was reading three volts. That told me the computer wasn’t able to extrapolate that the oxygen was maxed out at one volt, making the truck run very poorly. That’s the kind of thing I have to verify with a different testing device.
Diagnostics is like anything that requires a skill: You have to practice doing it on a regular basis or you lose it. It’s not like riding a bike—it’s a constant learning process.
If it’s slow throughout the day, I will test on known good cars at work, just because it’s beneficial to know what good vehicles look like. You can read blogs on the Internet or in a forum, but until you actually do it, you don’t really understand the process. Sometimes I’ll stay 15 or 20 minutes late after work just to play with something.
There’s really no stopping to learning when you’re a diagnostic tech. Even when I go home, I’m constantly learning. I spend off-time on iATN. I’m a member of Autonerdz. I watch lectures on YouTube. I read trade magazines. I’ll even call up other technicians throughout the day to bounce ideas off them. One person cannot possibly know everything. There’s just so many different variables in today’s cars that you need any bit of help you can get.
About the Author
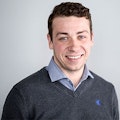