When it gets crowded, work can become a little uncomfortable. For Bob Ling, owner of Silverdale Autoworks in Silverdale, Wash., doubling the size of his shop allowed for more movement and area to work in for his employees.
The shop did not have a very large footprint at the time, he says, and it was important to expand on the size of the business. Prior to the shop’s two-part expansion beginning in early 2018, the auto repair shop sat at 2,000 square feet and housed five bays.
“It was tight, but we were still doing $1.6 million,” Ling says.
Today, the business has grown into a 4,000-square-foot facility, where Ling now has eight lifts positioned in the shop—comfortably.
Ling discusses how the decision to choose the right lift for his shop—one that wouldn’t take away space from the building—allowed staff members to work more comfortably on the shop floor as well as improve the shop’s overall aesthetic.
The Backstory
In 1994, Ling opened Silverdale Autoworks, an auto repair shop remotely located in Silverdale, Wash. Today, Ling oversees his staff throughout the day, and typically can be found assisting service technicians if they need any help. Lately, Ling says he’s been involved in finalizing the building’s renovation.
Before the expansion, Silverdale Autoworks housed five lifts throughout the shop, but space was tight.
“[The expansion] started in January of 2018 and we actually did it on the same piece of property that we’re working on,” Ling says. “We had to do it in two phases.”
According to Ling, they built four bays as well as an office, and once construction was completed on that side of the shop, the other half went under construction.
“We moved the techs from the old bays into the new bays and tore those four bays down to redo them,” Ling says. “It was the only way we could do it; I couldn’t shut down for a year.”
The Problem
“We had a very small footprint and it just wasn’t going to be feasible to put above-ground lifts [in the shop],” Ling says.
According to Ling, the width of the five above-ground lifts—at 10,000 pounds each—would pose more inconvenience for the shop, as well as occupy additional room on the shop floor.
“We would have had to stagger those lifts to get eight bays out of this footprint,” Ling says.
The prior setup also had an efficiency issue, Ling says. With above-ground lifts featured in the building’s small space, the lifts became tedious and created frustrating situations. For example, if you needed to move a piece of equipment from the front to the back of the car, you had to jack up the vehicle to move that piece of equipment, because there was no room to wheel it around the lifts.
“It was very inconvenient and it took more time,” Ling says.
The Solution
In order to avoid creating a clunky, disorganized space, Ling decided to invest in seven in-ground lifts that would take up less room. Since footprint was the shop’s biggest issue prior, Ling decided to swap out above-ground for in-ground lifts.
“The other advantage for in ground compared to above-ground lifts is that you don’t have the posts next to the doors, so you don’t get door dings [on vehicles],” Ling says.
By deciding to invest in an in-ground lift, he now had to choose between two companies.
“Both are great, but I chose Rotary because of the servicing,” Ling says. “We would get better servicing with the Rotary just based on who is available in our area.”
According to Ling, the shop is positioned in an out-of-the-way area, where the business is not necessarily close to any large cities. During the construction period, Ling had purchased an above-ground lift, Rotary Revolution, from a property across the street that the shop had leased.
“I read about lifts for years and I know they’re a real solid product,” Ling says. “For me, I’m more of a long-term kind of thinker; I always look for quality over price.”
Additionally, Ling connected with a supplier who does installation in his area and also is familiar with the lifts, and he suggested the lift for the same reason—parts are easier to get, Ling says.
The process for bringing in-ground lifts into a business is different than bringing in above-ground. According to Ling, in-ground lifts are placed in nine feet holes dug out of the ground. Later, the holes are filled with rock, dirt, and cement to seal the surface. Although Ling does not recall the exact amount of the installation fee, the total of the new seven lifts, Hunter alignment machine (that he purchased at the same time) and installation was around $120,000.
“It’s not hard to do, you just can’t do it yourself,” Ling laughs.
The whole process to digging holes, placing the lifts inside, and then pouring the cement took around two-and-a-half to three days from start to finish, Ling says. During the installation, he was able to still perform work in a portion of the shop and the leased property across the street.
The Aftermath
Since implementing the in-ground lifts, Ling has noticed more efficiency around the shop, he says. According to Ling, the pads where cars are lifted on are lower to the ground, so lower cars are able to get racked easier, he says.
“They’re much handier and they can get cars on easier,” Ling says.
Since there’s more space in the shop, Ling believes the shop environment is less stressful for employees.
“The guys like them better because they can get the vehicle on the lift faster without jostling the cars back and forth like we used to have to do. They don’t have to work under a dash when it’s on the rack and they don’t have the post to deal with,” Ling says. “Moving equipment is much easier and it’s much more agronomic all the way around.”
The Takeaway
When you’re deciding on new equipment for the shop, it’s critical to think long-term, Ling says.
“One of our biggest things is, ‘Can you get service?’ and depending on what kind of piece of equipment you buy—hit or miss—that’s a top thing to be thinking about,” he says.
About the Author
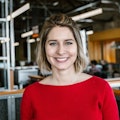