If you happen to be a baseball fan, I’m guessing you recognize the quote I used for this letter’s headline, right? It’s one of my favorites from the vast collection of confusingly inquisitive quotes left behind by Hall-of-Famer Yogi Berra. (Personal note: It also served as the “tagline” to my own column, back in my sportswriting days.)
All “Yogi-isms” should be taken with a “grin of salt” (another Yogi gem); that is, they’re a little off but more than just amusing. There’s truth in there.
Anyway, that quote in the headline above—you can observe a lot just by watching—popped into my head as I gave one final read to our cover story this month during our production process. The piece that Associate Editor Travis Bean put together (“The Apprenticeship Blueprint”) examines a very important strategy to solve what many see as a talent shortage in this industry. The more we examine recruiting and retaining talent in our magazine, the more we seem to find fairly uniform agreement from folks across the industry that apprenticeship programs (or variations on that concept) are a very focused approach to ensuring your operation has its own self-sustained pipeline of employees.
I love hearing stories like the ones that make up that feature—as well as countless others that frequent the pages of our magazine. These are people that see problems and face them head-on with solutions rather than excuses. They don’t see any option other than driving forward. It not only makes for a great story, but it also sets the example for others, regardless of the industry, to follow. And it sets the example to the rest of their teams within their operations.
Just as it helps young, up-and-coming technicians to shadow, watch and learn from experienced members of your teams, the rest of your team most likely looks to you to set that overall tone—the attitude and cultural foundations that shape the way everyone views obstacles as they appear. Whether it’s as daunting as a talent shortage or as trivial as a minor day-to-day mistake being made, your team will observe a lot just by watching your reaction.
Personally, I appreciate getting that reminder through so many of you that inspire me to do better each day in my own job. So, here’s to finding solutions, or as Yogi would say, “When you get to a fork in the road, take it.”
About the Author
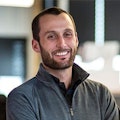
Bryce Evans
Bryce Evans is the vice president of content at 10 Missions Media, overseeing an award-winning team that produces FenderBender, Ratchet+Wrench and NOLN.