During some months, like winter times and back-to-school periods, Bridgwater finds that these slow days are more prevalent than others. Bridgwater has learned to deal with these issues, and as he admits, there are still months that were a struggle, especially last year. But this year, during the normal slow periods, his shop saw a significant boost in revenue, and he attributes much of this to his slow day procedure.
Bridgwater pays his employees by the hour and doesn’t send them home when they’re slow, so it’s vital that each employee is finding some kind of work in the shop to take on. Properly coping with a slow day starts from the management end of things, to make sure your staff doesn’t slack off and makes the most of their time. Bridgwater details his procedure to deal with slow times in his shop.
1. During the slow times, start by having a shop meeting to go over the goals for the day and the things you can do in the meantime. We try to have a shop meeting once per week anyway, but if we’re super busy, we might not have a chance to have that meeting. When we’re busy, we may have had a problem with this thing or that thing, and we can use the slow days to deal with that.
2. Take a critical look at any equipment maintenance or upkeep that can be done. We will discuss and see if we can put certain equipment together, and figure out a way to make that happen. Maybe we have this transmission flushing machine that we keep over on this side of the shop, and we have a draining machine and these fluids stuck in the middle. When we’re busy, of course we don’t have time to move stuff around and make that happen, so on the slow times, when we have a list of these things that we’ve thought of during the busy times, then we’ll be able to attack.
3. Making the shop more efficient and organized is another important thing to take on. The shop needs to be clean and organized so that when we are busy, we spend less time hunting for things.
4. Training should certainly be an emphasis during slower times—I want my staff to have all certifications they can possibly have. We’re gangbusters busy this week, but I sent one of my guys on Tuesday to go take his smog license exam, and sent another guy on Wednesday to take his brake license exam, even though we were very busy. So, in the slow times, we absolutely make an emphasis to fill it with things like that. There’s a lot of online learning we can do, there’s always something.
5. Software updates for scan tools is always an ongoing thing. If we have a slow day, we can go through tools, see if anything needs updating, or if we need to replace any specific equipment.
6. Service advisors should use slow days to reach out to customers that the shop hasn’t seen in a while. Right now we use AutoVitals, and some other workflow management stuff. That does a lot of reporting, and scours the database for us. That automation helps, but it doesn’t cover everything. We can have our service advisors reach out and say, we haven’t seen you in six months, have you had your services taken care of? Also, do they not like us for some reason? If not, why don’t they like us? How can we correct that? This can be a time to have those conversations.
These calls to customers often take up a lot of time, so you can make them during the slow days. Getting a hold of those customers is sometimes challenging, we’ll invite the client to call us back without leaving a detailed message: Hey, we had a question for you, some sort of a leading question or introduction.
About the Author
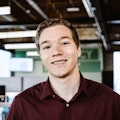